2025 ผู้เขียน: Howard Calhoun | [email protected]. แก้ไขล่าสุด: 2025-01-24 13:26
มีข้อบกพร่องของรางต่างๆ จำนวนมากพอสมควร พวกเขาทั้งหมดเกิดขึ้นด้วยเหตุผลที่แตกต่างกัน โดยรวมแล้วมีข้อบกพร่องสี่ประเภทหลักเนื่องจากการสลายเกิดขึ้น เทคโนโลยีการผลิตรางและการเชื่อมที่ไม่ดีเป็นสาเหตุแรกของการสึกหรอ เหตุผลที่สองคือเนื้อหาของเส้นทางต่ำเกินไป วัสดุมีพารามิเตอร์เช่นความต้านทานความล้าของหน้าสัมผัส และหากพารามิเตอร์นี้ไม่สูงพอ รางก็จะใช้งานไม่ได้เช่นกัน เหตุผลสุดท้ายสำหรับความล้มเหลวของสิ่งอำนวยความสะดวกเหล่านี้คือผลกระทบของหุ้นกลิ้งที่เคลื่อนผ่านพวกเขา
สาเหตุของความล้มเหลว
ระหว่างการใช้งาน ข้อบกพร่องของรางและเหตุการณ์ที่น่าจะเกิดขึ้นนั้นคำนวณจากข้อเท็จจริงหลายประการ ประการแรก ปัจจัยสำคัญคือปริมาณระวางน้ำหนักที่ไหลผ่านตลอดช่วงของเส้นทาง ประการที่สอง ภาระบนเพลาของสต็อกกลิ้งมีบทบาท ความเร็วของรถไฟยังส่งผลต่อสภาพของรางด้วย การปฏิบัติและสังเกตแสดงให้เห็นว่าในฤดูร้อนนั่นคือในฤดูใบไม้ผลิและฤดูร้อนจำนวนแทร็กที่ขาดจะลดลง ในฤดูใบไม้ร่วงตัวบ่งชี้นี้จะเพิ่มขึ้นเล็กน้อยและในฤดูหนาวจะเพิ่มขึ้น 2-3 เท่าเมื่อเทียบกับฤดูร้อน มีคำอธิบายสำหรับสิ่งนี้และอยู่ในความจริงที่ว่าที่อุณหภูมิต่ำโลหะนั้นมีความเปราะบางเพิ่มขึ้น กล่าวอีกนัยหนึ่ง แรงกระแทกจะลดลงเหลือน้อยที่สุด เปอร์เซ็นต์ที่ใหญ่ที่สุดของความล้มเหลวของรางอันเนื่องมาจากข้อบกพร่องของรางเกิดขึ้นในเดือนมีนาคม หากเราพูดถึงส่วนยุโรปของประเทศ และในเดือนเมษายน หากเกี่ยวข้องกับภูมิภาคตะวันออกและไซบีเรีย
เครื่องตรวจจับข้อบกพร่องใช้เพื่อตรวจจับปัญหาดังกล่าว 96.5% ของปัญหาที่ระบุทั้งหมดสามารถระบุได้โดยใช้อุปกรณ์ที่ถอดออกได้หรือแบบพกพา ตรวจพบอีก 2% โดยใช้เครื่องตรวจจับข้อบกพร่องของรถยนต์และอีก 1% ใช้อุปกรณ์รุ่นอื่นของอุปกรณ์นี้ เป็นสิ่งสำคัญมากที่จะต้องทราบว่ามีการจำแนกประเภทข้อบกพร่องของรางและคำอธิบายโดยใช้ตัวเลข สิ่งนี้ทำเพื่อให้สามารถดำเนินการบัญชีรางคงที่ได้
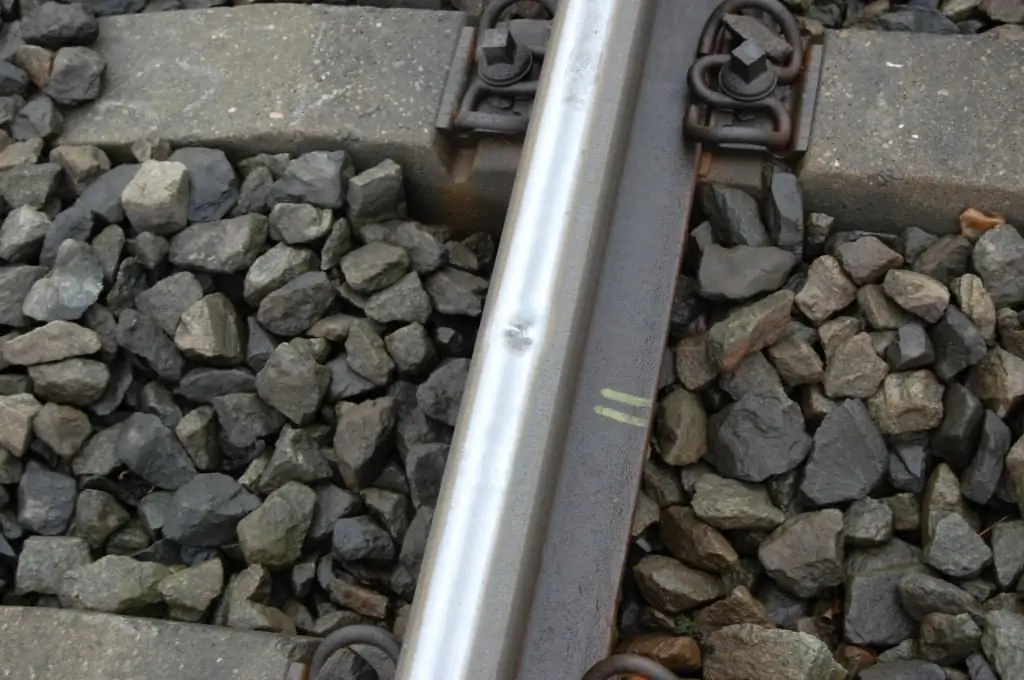
การจำแนก
ความเสียหาย การแตกหัก หรือข้อบกพร่องใด ๆ ในส่วนแทร็กจะถูกระบุโดยใช้ระบบตัวเลขแบบรวมศูนย์ ตัวเลขสองตัวแรกเป็นตัวหลักและตัวที่สามเป็นตัวเสริม ตัวเลขแรกระบุประเภทของข้อบกพร่องหรือความเสียหายของราง นอกจากนี้ยังระบุตำแหน่งของปัญหาในส่วนทางรถไฟอีกด้วย ตัวเลขตัวที่ 2 อธิบายประเภทของข้อบกพร่องหรืออธิบายความเสียหายโดยคำนึงถึงสาเหตุที่มันปรากฏขึ้น. ตัวเลขเสริมที่สามระบุตำแหน่งของข้อบกพร่องหรือความเสียหายตามความยาวของราง รายละเอียดเพิ่มเติม ข้อบกพร่องของรางและการจำแนกประเภทนั้นอธิบายด้วยตัวเลขตั้งแต่ 1 ถึง 9 สำหรับอักขระตัวแรก
- ถ้าตัวเลขแรกคือ 1 แสดงว่าโลหะมีรอยบิ่นและลอกบนผิวลูกกลิ้งของรางรถไฟ
- ถ้าเป็นเลข 2 แสดงว่าพบรอยร้าวตามขวางในหัวรางที่ส่วนของราง
- หมายเลข 3 ยังระบุถึงรอยแตกที่หัวราง แต่เป็นประเภทตามยาว
- หมายเลข 4 บ่งบอกว่ามีการเปลี่ยนแปลงของพลาสติก กล่าวคือ ถูกกดทับ แนวตั้ง ด้านข้าง หรือสวมศีรษะไม่เรียบ
- 5 คือความเสียหายของรางและตำหนิที่คอ
- 6 คือความล้มเหลวหรือความเสียหายต่อรางเท่านั้น
- 7 - นี่เป็นการเสียรูปที่ค่อนข้างแรง เนื่องจากตัวเลขนี้บ่งชี้ว่าเกิดการโก่งตัวตลอดช่วงของรางรถไฟ
- หากเกิดการแตกหักในระนาบแนวตั้งและแนวนอน ระบบจะกำหนดหมายเลข 8 แทนหมายเลขแรก
- รางอื่นๆ ชำรุด เสียหาย และอื่นๆ ที่ไม่จัดอยู่ในหมวดหมู่ใดๆ ข้างต้น จะแสดงด้วยหมายเลข 9
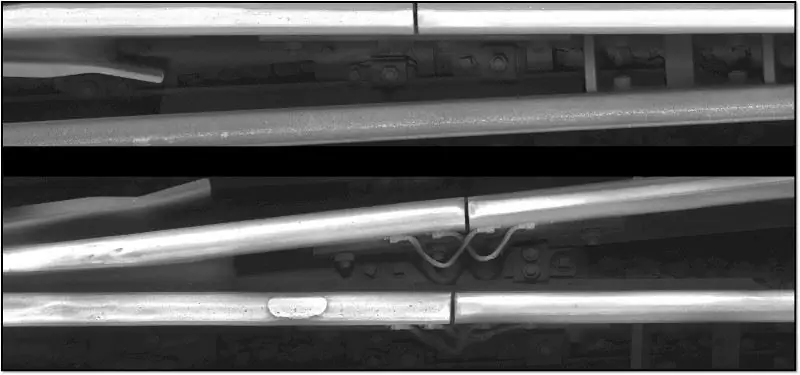
การกำหนดความหมายของตัวเลข
หมายเลขหลักที่สองสำหรับรหัสข้อบกพร่องของรางยังมีค่ามากมายให้แม่นยำยิ่งขึ้นตั้งแต่ 0 ถึง 9
- ถ้าหลักที่สองเป็น 0 แสดงว่าข้อบกพร่องเกิดขึ้นเนื่องจากการเบี่ยงเบนจากเทคโนโลยีในการสร้างส่วนนี้ของทางรถไฟการผลิต
- หมายเลข 1 บ่งบอกว่าคุณภาพโลหะของเหล็กที่ใช้ในการผลิตรางไม่เพียงพอ นอกจากนี้ยังเป็นไปได้ว่าความแข็งแรงของเหล็กจะต่ำกว่าที่จำเป็นสำหรับการทำงานปกติ
- 2 - ระบุว่ามีข้อผิดพลาดเกิดขึ้นระหว่างการประมวลผลส่วนท้าย เนื่องจากส่วนของเส้นทางล้มเหลว นอกจากนี้ยังรวมถึงข้อเสียบางประการที่เกิดขึ้นเมื่อประมวลผลโปรไฟล์ราง
- 3 - สิ่งเหล่านี้เป็นข้อบกพร่องในรางของรางรถไฟซึ่งเกิดขึ้นเนื่องจากข้อเท็จจริงที่ว่าข้อกำหนดของคำแนะนำสำหรับการบำรุงรักษาวัตถุในปัจจุบันถูกละเมิด นอกจากนี้ยังรวมถึงความเสียหายที่เกิดจากข้อเท็จจริงที่ว่าหลักการของเทคโนโลยีสำหรับการประมวลผลรูโบลต์ในโรงหลอมถูกละเมิด
- หากหมายเลขที่สองคือ 4 แสดงว่ามีปัญหากับรางเกิดขึ้นเนื่องจากผลกระทบเฉพาะกับรางเลื่อน เช่น เนื่องจากการลื่นไถล รวมถึงความเสียหายที่เกิดขึ้นเนื่องจากสต็อกกลิ้งไม่ผ่านการตรวจสอบที่เหมาะสม หรือมีการละเมิดโหมดการขับขี่
- หมายเลข 5 รวมความเสียหายทั้งหมดที่เกิดจากแรงกระแทกทางกลจากภายนอก เช่น การกระแทกเครื่องมือ การกระแทกรางกับราง เป็นต้น
- ข้อบกพร่องในการเชื่อมคอมมอนเรลที่ค่อนข้างธรรมดานั้นเกิดจากความผิดปกติในการทำงานของเครื่องเชื่อม เกิดขึ้นในรอยเชื่อมและหมายเลข 6
- 7 - ปัญหาที่เกี่ยวข้องกับการทำงานของรางที่ข้อต่อ
- 8 - สิ่งเหล่านี้เป็นข้อบกพร่องที่เกิดจากพื้นผิวของรางเช่นเดียวกับเนื่องจากการเชื่อมข้อต่อรางที่ไม่เหมาะสม
- ปัญหาที่เกิดจากการกัดกร่อนมีหมายเลข 9
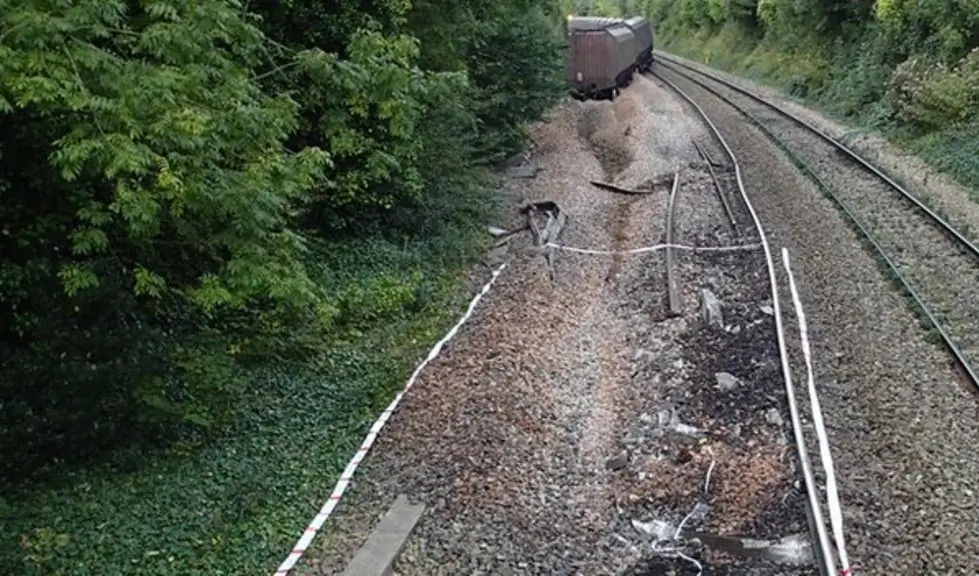
เป็นที่น่าสังเกตว่าความล้มเหลวของส่วนของรางเนื่องจากการพังทลายของรางเป็นผลมาจากผลกระทบของสาเหตุหลายประการในเวลาเดียวกัน บ่อยครั้งที่ปรากฎว่าการขาดการบำรุงรักษาทางรถไฟช่วยเร่งการพัฒนาข้อบกพร่องที่เกิดขึ้นระหว่างการประกอบหรือการเชื่อมโครงสร้างอย่างมาก ด้วยเหตุนี้จึงเป็นเรื่องยากที่จะระบุสาเหตุ เนื่องจากจำเป็นต้องค้นหาแหล่งที่มาหลักของการแยกย่อยอย่างแม่นยำ ข้อบกพร่องในรางของรางรถไฟหรือมากกว่านั้นการนับก็มีหลักที่สามเช่นกัน
- 0 แสดงว่ามีปัญหาตลอดแนวราง
- 1 หมายความว่าปัญหาอยู่ที่ข้อต่อในหลายจุด บางทีข้อต่อแบบเกลียวอาจหักซึ่งอยู่ห่างจากปลายรางอย่างน้อย 750 มม. หากเรากำลังพูดถึงรอยเชื่อม ที่ระยะ 200 มม. สมมาตร 100 มม. ในแต่ละด้านของแกนของแนวเชื่อม
- 2 แสดงว่าปัญหาอยู่นอกข้อต่อ หากเรากำลังพูดถึงการเชื่อมต่อแบบสลัก คุณต้องดูที่ระยะห่าง 440 มม. แบบสมมาตร 220 มม. ในแต่ละด้านของแกนของรอยเชื่อมในตีนรางรถไฟ
ข้อบกพร่องในการเชื่อมรางและความเสียหายอื่นๆ ยังแบ่งออกเป็นสี่ประเภท ขึ้นอยู่กับระดับของการพัฒนา มีดีกรีเป็น DP, D1, D2 และ D3 อันตรายที่สุดคือ DP การกำหนดนี้บ่งชี้ว่าความเสียหายได้มาถึงค่าหรือขนาดที่สำคัญ พื้นที่ดังกล่าวควรจะถูกแทนที่ก่อน ข้อบกพร่องที่จัดเป็น D1 และ D2 จะได้รับการแก้ไขตามขั้นตอนที่กำหนดไว้ซึ่งคำนึงถึงความรุนแรงของปัญหา รางที่มีข้อบกพร่องที่เกี่ยวข้องกับหมวด D3 จะถูกเปลี่ยนก็ต่อเมื่อส่วนหัวของระยะแทร็กตัดสินใจเช่นนั้น การตัดสินใจขึ้นอยู่กับข้อมูลที่ส่งโดยหัวหน้าคนงานหลังจากการตรวจสอบตามกำหนดเวลาและคำนึงถึงระดับของการพัฒนาข้อบกพร่อง เป็นผลให้ปรากฎว่ารหัสข้อบกพร่องของรางประกอบด้วยตัวเลขสามหลักรวมถึงตัวบ่งชี้ระดับของการพัฒนาในส่วนนี้
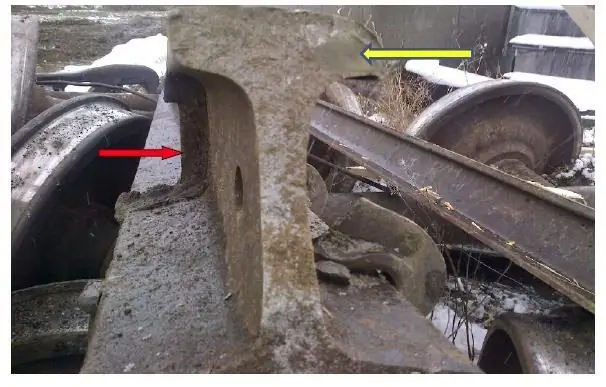
การตรวจจับข้อบกพร่อง
การตรวจจับข้อบกพร่องเป็นขั้นตอนในการระบุข้อบกพร่องในโครงสร้างของทางรถไฟโดยใช้อุปกรณ์ตรวจจับข้อบกพร่องพิเศษ เป็นที่น่าสังเกตว่ารางต้องผ่านขั้นตอนนี้หลายครั้ง การตรวจจับข้อบกพร่องครั้งแรกจะดำเนินการที่โรงงานรีดราง เมื่อจำเป็นต้องประเมินคุณภาพของงานที่ทำเสร็จแล้ว กระบวนการตรวจสอบครั้งต่อไปได้เกิดขึ้นแล้วในสภาพการทำงาน นั่นคือระหว่างทาง นอกจากนี้ การตรวจสอบยังดำเนินการในเวิร์กช็อปการเชื่อมราง ซึ่งกระบวนการเชื่อมไม่เพียงแต่ของใหม่ แต่ยังดำเนินการซ่อมแซมหรือเชื่อมโครงสร้างเก่าด้วย
ขั้นตอนการตรวจจับข้อบกพร่องมีวัตถุประสงค์หลักเพื่อระบุข้อบกพร่องของรางที่เป็นอันตรายซึ่งอยู่ภายในโครงสร้าง นั่นคือ ยังไม่มีข้อบกพร่องที่ด้านนอก ทำให้สามารถเปลี่ยนโครงสร้างที่เสียหายได้ทันท่วงที
ประเภทของปัญหา
ปัจจุบันข้อบกพร่องทุกประเภท วิธีกำจัด สาเหตุของการเกิดขึ้นวิธีการกำหนด ฯลฯ นำเสนอใน "เอกสารกำกับดูแลและทางเทคนิค NTD / TsP 2002" นอกจากนี้ยังเป็นที่น่าสังเกตว่ายังมีเอกสารการทดลองรวมถึงการจำแนกข้อบกพร่องของราง NTD / TsP 1-93 ตามที่ส่วนปัญหาทั้งหมดของทางรถไฟแบ่งออกเป็นข้อบกพร่องอย่างเฉียบพลัน (OD) และข้อบกพร่อง (D)). เป็นหมวดของข้อบกพร่อง D ด้วยความช่วยเหลือของ NTD / CPU 2002 ที่แบ่งออกเป็นหลายประเภทขึ้นอยู่กับสาเหตุของการเกิดขึ้นระดับการกระจายและตำแหน่งบนเส้นทาง
รางที่ชำรุดอย่างแหลมคมคือรางที่เป็นภัยโดยตรงต่อการเคลื่อนตัวของรถไฟ เพราะเนื่องจากอิทธิพลของข้อบกพร่อง รางเหล่านี้อาจยุบลงไปใต้ล้อของรถไฟหรือทำให้รถกลิ้งหลุดออกจากราง ติดตาม. หากพบส่วนดังกล่าวจะต้องเปลี่ยนเป็นส่วนใหม่หรือส่วนเก่าจากสต็อกกิโลเมตรทันที หากพบข้อบกพร่องใหม่ในรางรถไฟก่อนหมดระยะเวลารับประกันการใช้งาน หรือหากน้ำหนักผ่านน้อยกว่าที่ระบุไว้ในเอกสารประกอบ จะมีการร้องเรียนต่อโรงงานโลหะวิทยาที่ผลิตชิ้นส่วนดังกล่าว หากตรวจพบข้อบกพร่องที่รอยเชื่อมก่อนกำหนด การร้องเรียนจะถูกส่งไปยังโรงเชื่อมราง
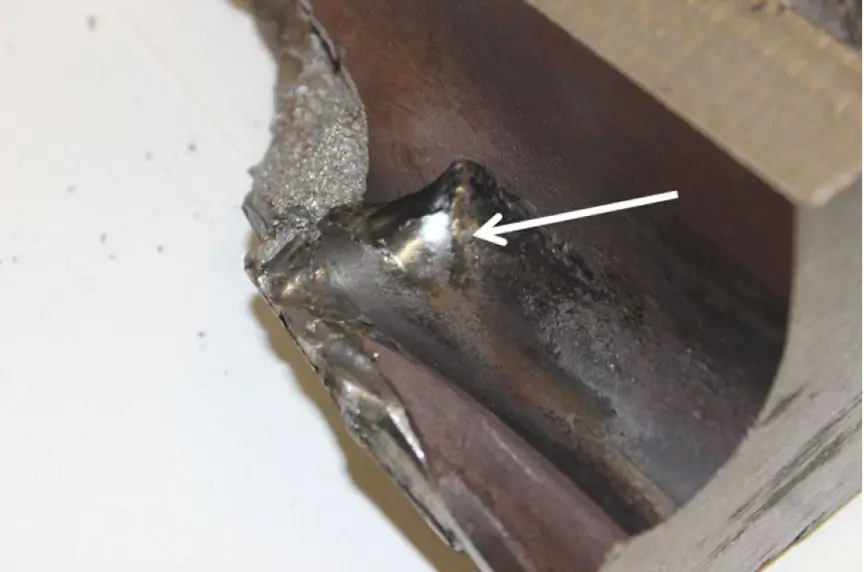
รางชำรุดรวมถึงส่วนของรางที่เริ่มใช้งานไม่ได้เนื่องจากอายุการใช้งานที่ยาวนาน คาดว่าจะเกิดข้อบกพร่องในพื้นที่ดังกล่าว อย่างไรก็ตาม พวกเขายังคงต้องแน่ใจว่าได้ผ่านพ้นไปได้อย่างปลอดภัย แม้ว่าในในบางกรณี จะมีการจำกัดความเร็วเมื่อผ่านส่วนดังกล่าวของเส้นทาง ข้อบกพร่องของรางรุ่นใหม่และการจำแนกประเภทถูกนำเสนออย่างแม่นยำในเอกสารเชิงบรรทัดฐานและทางเทคนิค NTD / CPU 2002 ค่ารหัสของปัญหาที่เป็นไปได้ถูกนำเสนอด้านบน
แยกออกเป็นส่วนที่บกพร่องและบกพร่องอย่างมาก
เอกสารระบุความเร็วที่รถไฟสามารถเคลื่อนไปตามส่วนใดส่วนหนึ่งของรางรถไฟได้ หากระดับของการพัฒนาข้อบกพร่องอยู่ในกลุ่ม DP ความเร็วในการเคลื่อนที่จะไม่เกิน 40 กม. / ชม. จนกว่าจะถึงเวลากำจัด ประเภท D1 ให้ความเร็วไม่เกิน 70 กม. / ชม. D2 - ไม่เกิน 100 กม. / ชม. ข้อบกพร่องของกลุ่ม D3 ไม่ได้สร้างการจำกัดความเร็วของการเคลื่อนไหวของสต็อกกลิ้ง
นอกจากนี้ยังมีกรอบเวลาที่กำหนดสำหรับการเปลี่ยนรางที่ชำรุดแต่ละกลุ่ม หากไม่มีการเปลี่ยนตัวภายในระยะเวลาที่กำหนด หมวดหมู่จะถูกแทนที่ด้วยประเภทที่สูงกว่า กล่าวอีกนัยหนึ่ง DP3 ไปที่ D2, D2 ถึง D1, D1 ถึง DP โดยปกติ ในการเปลี่ยนแต่ละครั้ง กำหนดเวลาการเปลี่ยนจะเข้มงวดยิ่งขึ้น และการจำกัดความเร็วสำหรับการเคลื่อนไหวก็เพิ่มขึ้นตามบรรทัดฐานที่กำหนดไว้
ข้อบกพร่องในรางและการจำแนกประเภทใหม่ตาม NTD/CPU ยังกำหนดปัญหาที่เปลี่ยนส่วนของแทร็กให้กลายเป็นแทร็กที่มีข้อบกพร่องอย่างเฉียบพลันหรือเพียงแค่ชำรุด ถึง OD เป็นปัญหาเช่น:
- การเกิดขึ้นของรอยแตกตามขวาง ตามยาว หรือด้านข้างที่หัวราง ส่วนใหญ่แล้ว การแยกย่อยอยู่ในกลุ่มที่สองและสาม และรหัสของพวกเขาคือ 20, 21, 24, 25
- แตกในรูสลักด้วยรหัส 53 เช่นเดียวกับรอยแตกที่คอรางโดยไม่คำนึงถึงขนาดรวมถึงรหัส 50, 55, 59 และ 56.1.
- การสึกกร่อนหรือการสึกหรอเฉพาะที่ของรางที่มีรอยแตกรหัส 69 ที่เกิดขึ้นเนื่องจากความล้าจากการกัดกร่อน การบิ่นจากพื้นรางที่มีรหัส 60, 64, 65, 66 รวมถึงรอยร้าวตามขวางของราง
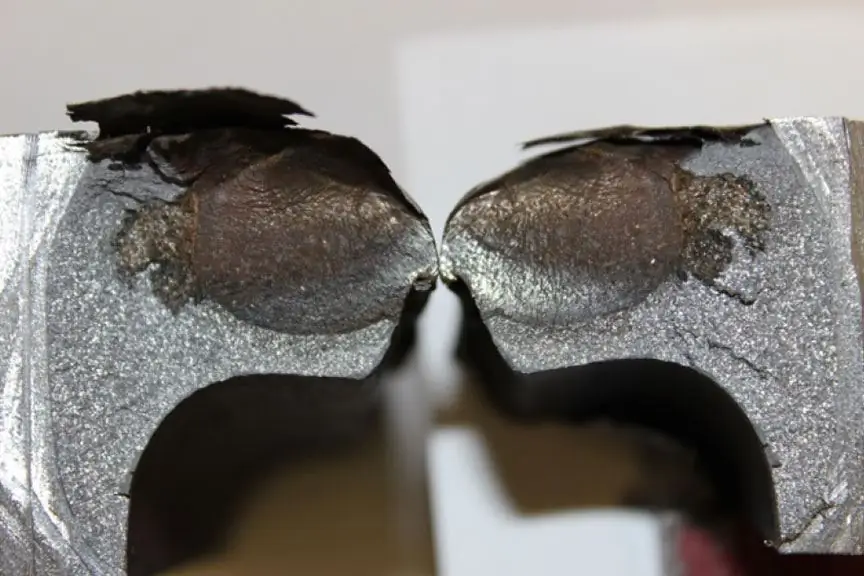
การเกิดขึ้นของข้อบกพร่องใหม่เหล่านี้นำไปสู่ความจริงที่ว่าแม้ส่วนใหม่ของทางรถไฟจะเข้าสู่สถานะ ML และต้องเปลี่ยนอย่างเร่งด่วน มีสัญญาณหลายอย่างที่ระบุรางที่ชำรุดในรางรับและออก ซึ่งรวมถึง:
- เกินรหัสลดมาตรฐาน 41+44 รหัสข้าง 44 หรือสวมหัวรางแนวตั้ง
- เศษโลหะ ถ้าความลึกไม่เกิน 3 มม. และยาว 25 มม.
- มีการเลื่อนหลุดจากล้อเลื่อน, การสึกหรอแบบลูกคลื่น
นอกจากนี้ยังเพิ่มด้วยว่าเปอร์เซ็นต์ที่ใหญ่ที่สุดของการเปลี่ยนรางปกติไปยังประเภทที่บกพร่องเกิดขึ้นเนื่องจากวัสดุขาดความแข็งแรงเมื่อสัมผัสเมื่อยล้า ปัญหาดังกล่าวของข้อบกพร่องในรางและส่วนประกอบผลิตภัณฑ์ซึ่งติดตั้งบนรางด้วยนั้นจัดอยู่ในประเภทรหัส 11 และ 21 และบ่อยครั้งที่สาเหตุก็คือปัญหา 44 ซึ่งหมายถึงการสึกหรอด้านข้างอย่างรุนแรงของส่วนหัวราง บ่อยครั้งที่มีการกัดกร่อนของพื้นราง - 69.
ข้อบกพร่องและสาเหตุโดยเฉพาะอย่างยิ่งอันตราย
ก่อนอื่นในการตรวจสอบรางต้องให้ความสนใจกับการพังทลายที่เกิดจาก"ความล้า" ของโลหะ ถือว่าอันตรายที่สุด ในรายละเอียดเพิ่มเติมดูเหมือนว่านี้ ล้อรถไฟสัมผัสกับรางบนพื้นที่ที่ค่อนข้างเล็กระหว่างการเคลื่อนไหว ผ่านพื้นที่เล็กๆ แห่งนี้ที่ส่งแรงดันไฟฟ้าจำนวนมหาศาลที่รถไฟเคลื่อนที่สร้างขึ้น เป็นแรงกดสัมผัสเหล่านี้ โดยเฉพาะอย่างยิ่งหากเกิดขึ้นในบริเวณใกล้เคียงกับส่วนหัวของราง ทำให้เกิดการบิ่นหรือทำให้เกิดการหลุดร่อนของโลหะ ยิ่งล้อผ่านบริเวณนี้มากเท่าไหร่ โลหะก็จะยิ่ง "เหนื่อย" มากขึ้นเท่านั้น เป็นเพราะเหตุนี้ข้อบกพร่อง 11.1-2 เกิดจากปัญหาเช่นความแข็งแรงในการสัมผัสต่ำของวัสดุ เพื่อหลีกเลี่ยงปัญหานี้ หรืออย่างน้อยเพื่อให้รางรองรับการเคลื่อนไหวมากขึ้น จำเป็นต้องเพิ่มความแข็งแรงของวัตถุดิบ
การหลุดลอกหรือการหลุดลอกของโลหะอาจเกิดจากการปรากฏของเส้นผม พระอาทิตย์ตก หรือกรงขัง ซึ่งอาจปรากฏบนพื้นผิวของรางในระหว่างการกลิ้ง
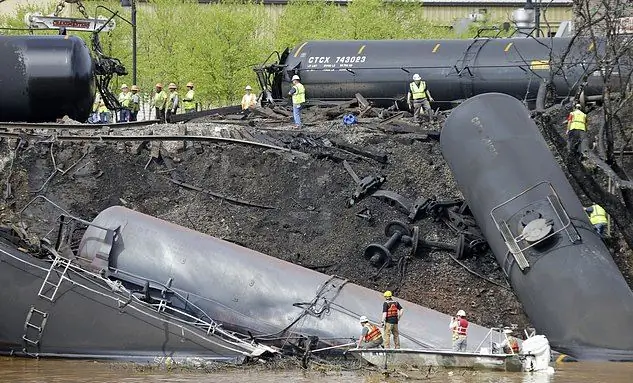
รางชำรุดกลุ่มดังกล่าวเป็น 20.1-2 และ 21.1-2 ถือว่าอันตรายมาก สำหรับข้อบกพร่องกลุ่มที่สองมักปรากฏในรูปแบบของรอยแตกภายในที่ศีรษะหรือรอยแตกภายนอกที่ปรากฏในบริเวณเนื้อในหัว หากเกิดปัญหาดังกล่าว รางอาจแตกในเวลาต่อมาภายใต้น้ำหนักของรถไฟที่กำลังเคลื่อนที่เป็นชิ้นเล็กๆ จำนวนมาก โดยธรรมชาติแล้ว สิ่งนี้จะนำไปสู่อุบัติเหตุและเป็นไปได้มากว่ารถไฟจะหลุดออกจากราง ส่วนปัญหารหัส 20.1-2 ก็เกิดขึ้นในหัวของมันเอง และเหตุผลหลักที่ทำให้รูปลักษณ์ของพวกเขาคือข้อบกพร่องของเทคโนโลยีการผลิต
ทางรถไฟชำรุดเนื่องจากการตรวจสอบไม่ดี
เป็นที่น่าสังเกตว่าเมื่อวันที่ 23 ตุลาคม 2014 การจำแนกประเภทข้อบกพร่องของราง 2499 NTD / CPU ได้รับการอนุมัติแล้ว เอกสารนี้มีผลบังคับใช้เมื่อวันที่ 1 กันยายน 2015 และเอกสารนี้มี 140 หน้า นอกจากนี้ยังมีการนำคำแนะนำใหม่เกี่ยวกับการบำรุงรักษาแทร็ก 2288 มาใช้ เอกสารนี้มีผลบังคับใช้เมื่อวันที่ 2017-01-03
ข้อบกพร่องเช่น 11.1-2 และ 21.1-2 ก็มักเกิดจากการที่หัวหน้าคนงานตรวจตราสภาพรางไม่ดี หากในช่วงแรกของการทำงานมีความลาดเอียงของรางที่ไม่ถูกต้อง ความเค้นหลักจะเปลี่ยนจากศูนย์กลางของส่วนไปยังขอบที่ส่วนหัวตั้งอยู่ ซึ่งแน่นอนว่าจะนำไปสู่การสึกหรออย่างรวดเร็ว ความถี่ของการเกิดข้อบกพร่องจะเพิ่มขึ้นอย่างมากหากมีการละเมิดความเรียบของเกลียวของราง นอกจากนี้ เป็นสิ่งสำคัญที่จะต้องทราบว่ากระบวนการของการเติบโตของปัญหาเหล่านี้มีความเกี่ยวข้องอย่างยิ่งไม่เพียงกับการบำรุงรักษารางรถไฟที่ไม่เหมาะสม แต่ยังรวมถึงการละเมิดในการดูแลส่วนที่กลิ้งของตัวรถไฟด้วย หากล้อรถบิ่น สไลเดอร์และตำหนิอื่นๆ จะส่งผลกระทบอย่างมากต่อความล้าของโลหะและการพัฒนา
นอกจากหัวแล้วปัญหามักเกิดขึ้นที่คอราง - รอยร้าวบริเวณรูน๊อตปัญหาหลัก ส่วนใหญ่แล้วรอยแตกจะเกิดขึ้นในรูปร่างของการเชื่อมต่อแบบเกลียวแล้วทิ้งไว้ที่ความลาดชัน 45 องศาถึงขอบฟ้า วิธีที่มีประสิทธิภาพในการต่อสู้กับรอยแตกดังกล่าวคือเนื้อหาที่มีคุณภาพของข้อต่อ กล่าวอีกนัยหนึ่งจำเป็นต้องขันสลักเกลียวให้แน่นที่สุดเพื่อป้องกันการหย่อนคล้อยของรางหรือการทรุดตัวของราง รอยแตกที่คอมักปรากฏขึ้นในบริเวณที่หัวรางผ่านเข้าไปในพื้นรองเท้า สาเหตุหลักที่ทำให้เกิดข้อบกพร่องดังกล่าวคือการเลือกรางใต้รางที่ไม่ถูกต้อง
สำหรับพื้นรองเท้าเอง ที่นี่ส่วนใหญ่ไม่เพียงแต่มีรอยร้าว แต่ยังรวมถึงรอยเจาะ เส้นผมด้วย ทั้งหมดนี้นำไปสู่การแตกในรางรถไฟ ทำให้เกิดรอยแตกตามยาว และเร่งกระบวนการกัดกร่อน วิธีที่ดีที่สุดในการจัดการกับข้อบกพร่องที่พื้นรองเท้าจำนวนมากคือการติดตั้งแผ่นรองที่ยืดหยุ่นได้ซึ่งวางไว้ใต้รางโดยตรง
ตำแหน่งของข้อบกพร่องและชื่อ
ปัจจุบันมีโต๊ะค่อนข้างใหญ่ที่บ่งบอกถึงข้อบกพร่องของรางหลักที่อาจเกิดขึ้นได้ พวกเขายังระบุสถานที่ที่เกิดความเสียหายนี้หรือว่ารหัสปัญหาถูกระบุอย่างแม่นยำ ตารางดังกล่าวมีลักษณะเช่นนี้
คำอธิบายปัญหา | สถานที่เสียหายบนราง | รหัสข้อบกพร่อง |
เนื่องจากการละเมิดเทคโนโลยีการผลิตราง อาจเกิดปัญหา เช่น รอยร้าวหรือการบิ่นของโลหะบนพื้นผิวที่ม้วนงอได้ | เข้าออกข้อต่อ | ขึ้นอยู่กับสถานที่ รหัสสามารถเป็น 10.1 หรือ 10.2 ตามลำดับ |
รอยแตกหรือบิ่นก็อาจเกิดขึ้นที่ด้านข้างของศีรษะหรือบนเนื้อ เกิดขึ้นจากภายในภายใต้อิทธิพลของการสะสมอโลหะจำนวนมาก | เข้าออกข้อต่อ | เช่นในกรณีก่อนหน้านี้ รหัสสามารถเป็น 11.1 หรือ 11.2 ขึ้นอยู่กับตำแหน่งของความเสียหาย |
โลหะอาจบิ่นที่พื้นผิวดอกยาง เหตุผลก็คือเอฟเฟกต์ไดนามิกในข้อต่อของสลักเกลียวเพิ่มขึ้น | อยู่ในทางแยก | รหัสความเสียหายนี้คือ 13.1 |
โลหะอาจเกิดการหกเลอะเทอะที่พื้นผิวดอกยางของหัวในบริเวณรอยต่อหลังจากปริมาณน้ำหนักที่ผ่านภายใต้การรับประกันหมดอายุ | รอยเชื่อมราง | รหัสข้อบกพร่อง 16.3 และ 16.4 |
ปัญหาการหกล้มคล้าย ๆ กัน แต่ก่อนที่ระวางน้ำหนักที่ค้ำประกันจะผ่านรางรถไฟ | รอยเชื่อม | ข้อบกพร่อง 17.3 และ 17.4 |
อาจเกิดรอยแตกตามขวางที่ศีรษะภายใต้อิทธิพลของผลกระทบทางความร้อนจากเครื่องกลจากการลื่นไถลหรือลื่นไถล เช่น | เกิดขึ้นทั้งในและนอกตะเข็บ | 24.1 และ 24.2 |
เนื่องจากการละเมิดเทคโนโลยีการเชื่อมหรือการละเมิดในการประมวลผลของรอยเชื่อม รอยแตกตามขวางอาจเกิดขึ้นในหัว สิ่งสำคัญคือต้องเพิ่มว่าสิ่งนี้สามารถนำไปสู่ความล้มเหลวของรางทันทีหลังจากพลาดการรับประกันน้ำหนัก | รอยเชื่อม | 26.3 และ 26.4 |
หากเกิดปัญหาแบบเดิมแต่ข้ามไปก่อนรับประกันน้ำหนักแล้วปัญหาจะย้ายไปหมวดอื่น | รอยเชื่อมยังคงเป็นที่ตั้ง | รหัสข้อผิดพลาดเปลี่ยนเป็น 27.3 และ 27.4 |
หากเทคโนโลยีการผลิตรางถูกละเมิด อาจเกิดรอยร้าวตามยาวหรือตามขวางในส่วนหัวของราง | สิ่งนี้เกิดขึ้นทั้งในข้อต่อและนอกข้อต่อ | รหัสความเสียหาย 30.1 หรือ 30.2 |
การพิจารณาข้อบกพร่องทางรถไฟ
วันนี้ วิธีเดียวที่ช่วยให้คุณตรวจจับข้อบกพร่องใหม่ในรางรถไฟได้ในระยะแรกและป้องกันคือวิธีอัลตราโซนิก
วิธีการทดสอบแบบไม่ทำลายนี้สามารถตรวจจับความเสียหายในรางโลหะได้โดยใช้คลื่นอัลตราโซนิก วิธีนี้ใช้ในหลายอุตสาหกรรมที่มีการทำงานกับโลหะ แต่วิธีนี้เป็นที่นิยมมากที่สุดในสถานีรถไฟ ซึ่งเป็นสิ่งสำคัญที่สุดในการตรวจสอบคุณภาพของรางรถไฟ การตรวจจับข้อบกพร่องด้วยคลื่นเสียงความถี่สูงจะช่วยให้ผู้ปฏิบัติงานระบุความเสียหายที่ซ่อนอยู่ได้อย่างรวดเร็วและแม่นยำ โดยจะไม่ส่งผลกระทบหรือทำลายวัตถุของการศึกษา
วิธีการตรวจหาข้อบกพร่องของรางนี้มีข้อดีหลายประการที่ปฏิเสธไม่ได้
อย่างแรกและที่สำคัญที่สุดคือไม่มีความเสียหายหรือเครื่องหมายอื่นใดหลงเหลืออยู่บนชิ้นทดสอบ เช่น ข้อบกพร่องใหม่ ประการที่สอง ค่าใช้จ่ายของอุปกรณ์ดังกล่าวค่อนข้างต่ำ และความน่าเชื่อถือของข้อมูลที่ได้รับจากการใช้งานนั้นสูงมาก ยิ่งไปกว่านั้น ที่สำคัญพอที่อุปกรณ์ดังกล่าวช่วยให้คุณค้นหาข้อบกพร่องของรางใหม่ได้ตลอดเวลาของปี ซึ่งเป็นสิ่งสำคัญอย่างยิ่ง
วิธีอัลตราโซนิกในการตรวจจับข้อบกพร่องช่วยให้คุณพบความเสียหายแม้เพียงเล็กน้อยในผลิตภัณฑ์โลหะและข้อต่อ ด้วยเหตุนี้ จึงใช้เพื่อตรวจสอบผลิตภัณฑ์และรอยเชื่อมโครงสร้าง การใช้อุปกรณ์อัลตราโซนิกสามารถระบุความเสียหายดังต่อไปนี้: การเกิดขึ้นของการละเมิดในความเป็นเนื้อเดียวกันของโครงสร้าง ตรวจสอบสถานที่ที่เสียหายจากการกัดกร่อน ตรวจสอบว่าองค์ประกอบทางเคมีของรางตรงกับที่ระบุในเอกสารหรือไม่